The Angle Grinder Wheels You Need for Fabrication
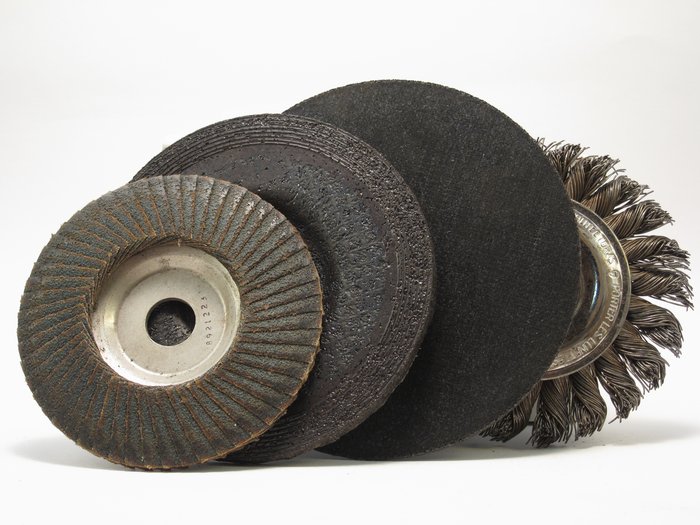
If you're doing fabrication, you need four types of wheels for your angle grinder. They are the standard grinding wheel, the flap disc, the cutoff wheel, and the wire wheel. If you scroll to the bottom of the article, you can see what each of these wheels does to a piece of rusty metal.
Angle grinder wheels are consumables: they last for a certain amount of time and then they need to be replaced. We've experimented with super cheap versions of angle grinder wheels and find that they don't last as long and don't hold together as well as versions that cost a little bit more. Here are a few that we've tried and liked:
We also like products from Norton, Gemini, and Milwaukee.
The Grinding Wheel
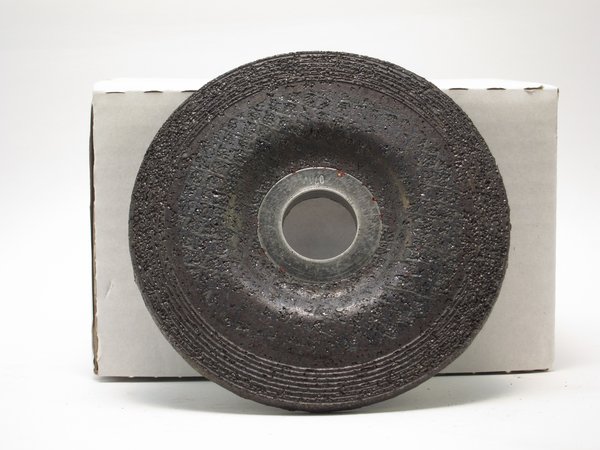
You can grind with this grinding wheel anywhere on the face or the edge of the grinding wheel.
The Angle Grinder Wheel for Fast Material Removal
The standard grinding wheel is all about fast metal removal. Use the grinding
wheel if you want to grind out welds, clean up cuts, and prep metal for
welding (since you need bare shiny metal to weld). Of the four wheels,
this removes material the fastest. It also produces hot, large sparks. Be sure that the sparks are not hitting anything you care about. Sparks will melt and embed into glass, burn holes in some clothing, and can be a little painful on your skin.
Grinding wheels come in different grits. Just like sandpaper, lower numbers (like 40 grit) are coarse and remove
material faster. We will caution that the lower the grit, the larger, hotter, and more painful the sparks are. While this is fine if you're working at a workbench, grinding under a 4x4 in an awkward position can become very uncomfortable with low grit wheels. Even with typical safety gear, it's harder to protect your body, your ears, and your eyes from bouncing sparks when you're jammed under your vehicle, so we suggest a higher grit wheel for that type of work. Stray sparks can easily ricochet and bounce behind a face shield/goggle combination. A higher grit wheel will take a little longer, but it's safer and more comfortable.
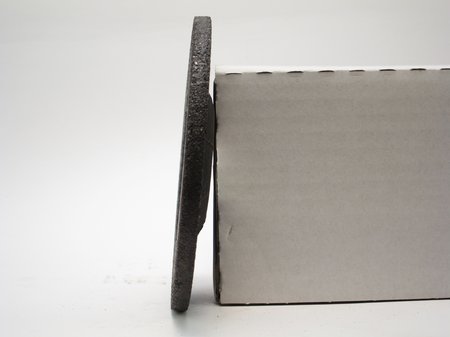
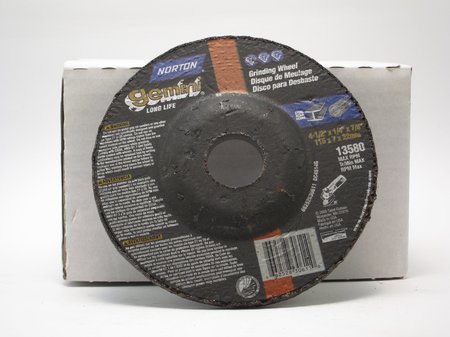
Standard grinding wheels are ideal for quick metal removal using your angle grinder. 1/4" thick is pretty standard for most grinding wheels.
Pay attention to the wheel diameter when buying grinding wheels. Make sure the wheels you get fit inside your grinder's guard.
We buy angle grinder grinding wheels 5-10 at a time and that quantity can do most of the typical fabrication projects on a single truck.
Low grit grinding wheels can leave "scratches" in your metal. Really coarse grinding wheels can also leave slight burrs on the edge of your workpiece. We usually clean up these scratches by using a flap disc (below) on the affected areas until the metal is smooth and shiny.
The Best Angle Grinder Wheel for Sharpening Mower Blades and Other Tools
This is also the angle grinder wheel you should use for sharpening mower blades, shovels, and other "blunt" garden tools. It's easy to remove your mower blade, put it in a bench vise, and sharpen it with your angle grinder. We often finish a blade with a flap disc to make sure it's smooth.
The Flap Disc is for Finishing

Flap discs are ideal when you want to sand metal with your angle grinder. They can lightly chamfer edges, remove burrs, and take the sharp edges off corners.
The Best Sanding Wheels for Angle Grinders
The grinding wheels above tend to gouge the material you're working on, but a flap disc smooths it out. While the grinding wheel is a hard composite material, the flap disc is basically just overlapping rectangles of sand paper. If you were to run your grinding wheel over an edge on a piece of steel, then you ran your fingernail over that spot, it would catch, since the grinding wheel will push out material at it’s leading edge. This is a burr. Burrs look bad, and can be sharp - they'll easily cut unprotected hands. The flap disc works great to clean up burrs and shine up gouged metal.
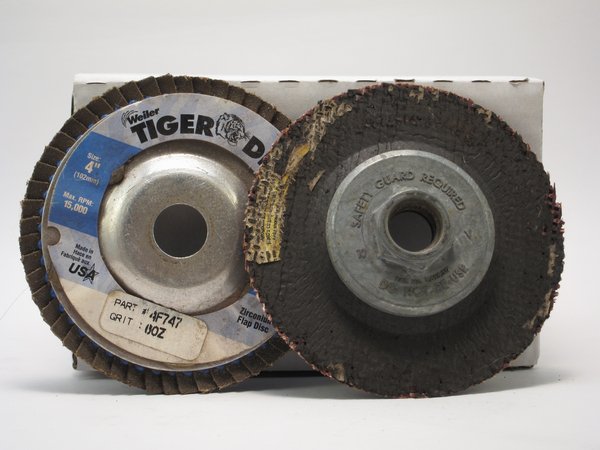
Use flap discs for finer metal sanding.
Like the standard grinding wheel, these come in different grits. Like
sandpaper, the higher grits are for fine work and the coarse grits are
for rougher work. We use flap discs all the time for finishing heavy
grinding. Flap discs make a huge difference in what your finished piece
looks like by removing burrs and scratches, allowing you to put slight
chamfers on edges, and also making it easy to take the hard edge off
corners.
The Cutoff Wheel is for Metal Cutting
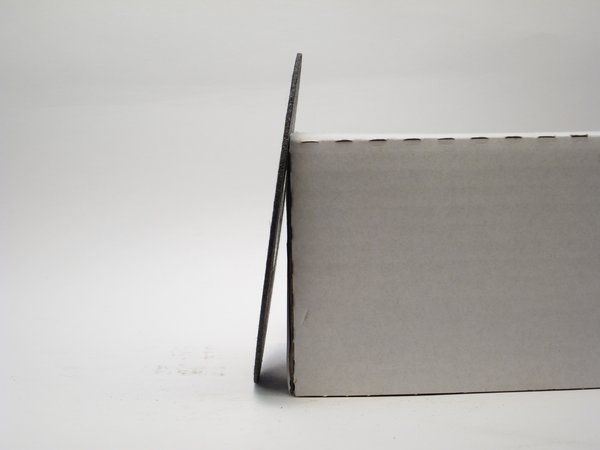
The thinness of a cutoff wheel is what makes it cut so easily through metal. This one is .045" thick.
The Best Angle Grinder Wheel for Cutting Metal
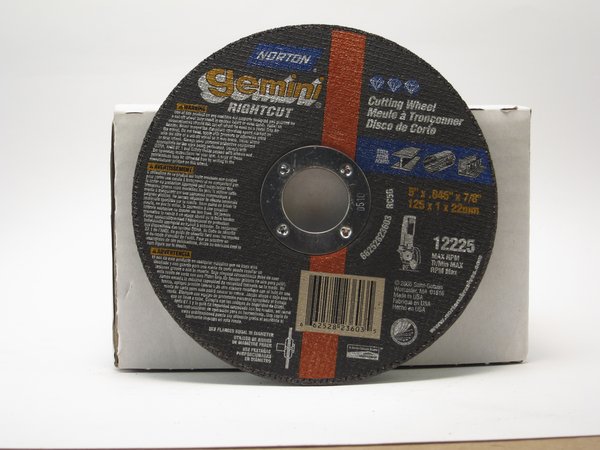
Cutoff wheels with a 7/8" arbor fit a special shoulder on angle grinders that have a 5/8"-11 threaded arbor.
The cutoff wheel is used for cutting metal. You can use it for cutting out welds, cutting small parts out of sheet or plate metal, or shortening bolts. You only use the edge of the wheel, not the back or front face. In fact, using either face will weaken a cuttoff wheel since they are so thin and the fibers that hold the wheel together are so exposed.
Cutting wheels are considerably thinner than standard grinding wheels. Typically, you'll use something that's either 1/8" or 0.045" thick. This is 1/2 to 1/4 as thick as a 1/4" grinding wheel. Because of their thinness and the fact that they only cut at the edge, they can cut metal extremely quickly.
The best angle grinder cutting wheels for metal are also the thinnest.
However, the thinner the wheel, the more dangerous they are. Thin
cutting wheels flex more easily and thus shatter more easily. If you're working at a work bench in a comfortable position with a well-positioned workpiece, a thin cutoff wheel is fine. If you plan to work under a vehicle in an awkward position, we recommend using a 1/8" cutoff wheel that is a little more rigid and will resist shattering if you lose your balance or position.
Also the Most Dangerous Angle Grinder Wheel...
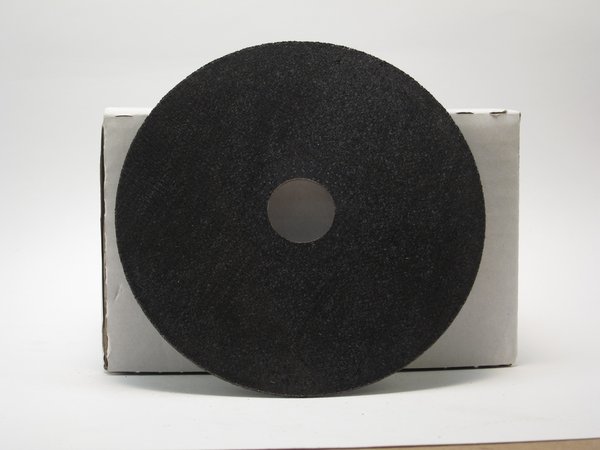
When you need to cut metal, a cutoff wheel on your angle grinder gets the job done quickly.
While the cutoff wheel is very, very handy, it is an extremely dangerous
wheel because it’s thin. If you twitch, lose your balance, or
otherwise accidentally twist the grinder while using this wheel, it will shatter.
The projectiles that fly off could break your nose, damage your hands,
hurt bystanders, etc. Keep your face away from this and out of the
plane of the spinning wheel.
We have shattered perhaps one
or two standard 1/4" grinding wheels in several years of fab work, but we've
shattered many cutoff wheels. Lots of fabricators have injuries from not
wearing proper safety gear or using cutoff wheels unsafely. One of us
even has a nice scar and some grinding material permanently embedded
under a fingernail after a shattered cutoff wheel impacted his hand and
shattered his fingernail. It's tough to get everything set up perfectly
for using a cutoff wheel on an angle grinder, so do the best you can and
wear lots of safety gear.
Safety glasses, face mask, grinder guard, heavy gloves, and no bystanders are essential when you spin up this wheel. We recommend not using a cutoff wheel unless both ends of your material are properly supported. Otherwise, the hanging piece may to pinch the spinning wheel and shatter it. A chop saw should instead be used for some types of work, like shortening lengths of tubing or angle iron.
The Wire Wheel is for Cleaning
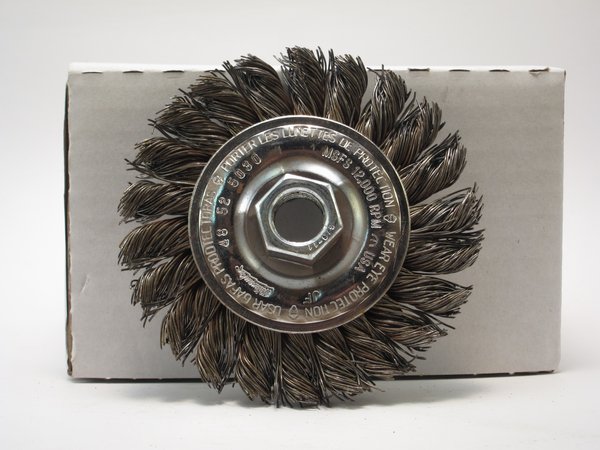
We like threaded arbors for wire wheels since they make it easy to take the wheel on and off.
The Best Angle Grinder Wheel for Cleaning Paint and Rust
Wire wheels are excellent for removing surface rust and paint. The
most abrasive wire wheels have thick, twisted bristles.
Straight and thin bristles are much less abrasive, but aren’t aggressive
enough if you need to do fast paint and rust removal. In fact, all of the wire wheels we use for our angle grinders are twisted. We only use straight bristle wire wheels on drill attachments and die grinders, and they are all small diameter.
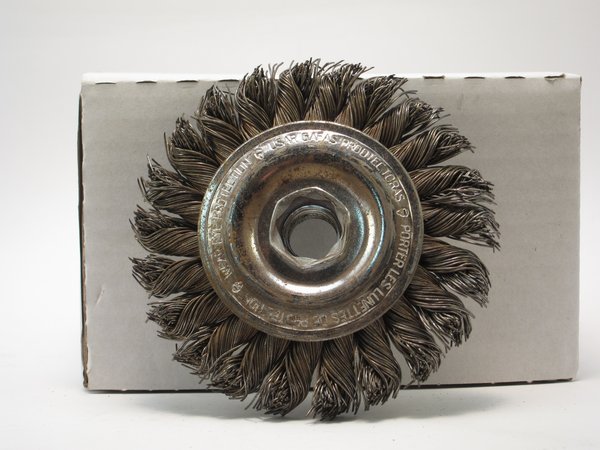
These are thick, twisted bristles, so this will be an aggressive wheel. This is the best type of wire wheel for heavy paint and rust removal.
Like the other wheels, stuff can fly off this wheel at high speeds - the wires occasionally break loose hard enough to stick in your skin. This isn’t so bad, but that should encourage you to wear eye protection. Don't buy cheap wire wheels for your angle grinder. We've tried wire wheels from Harbor Freight, and besides not lasting very long, they will spray you with wire filaments for as long as the wire wheel lasts. Besides being intolerably annoying, this is also dangerous for you and anyone around you since the filaments can so easily pierce skin (and certainly eyeballs).
Real World Tests: What These Grinding Wheels Do
Angle Grinder Wire Wheel Sample
The wire wheel easily took off the rust scale. If you were going to stick weld an emergency repair with 6010/6011 rod, this would probably be clean enough for the weld process. However, you’d want bare, shiny, clean metal for MIG or TIG. A wire wheel with steel bristles won’t gouge steel (although it might “soften” the appearance), but it can gouge softer metals like aluminum or brass.
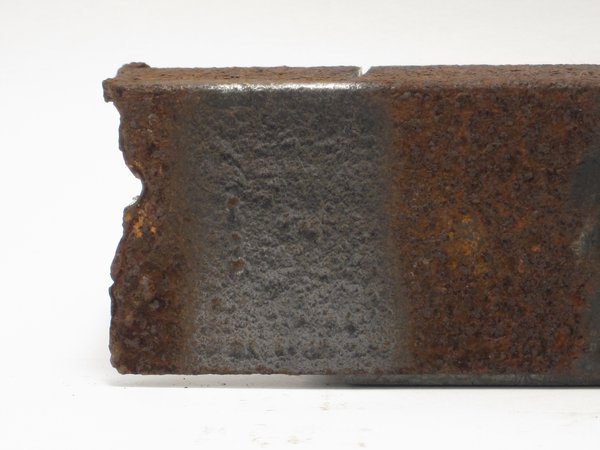
We prefer to have shiny metal for welding, but for a lot of projects a wire wheel will take off enough rust to later do a reasonable paint job.
Angle Grinder Flap Disc Sample
The flap disc is basically worthless for rust removal unless it’s just flash rusting. Scale comes off slowly and we never get to clean bare metal, so this is a pretty pointless use.
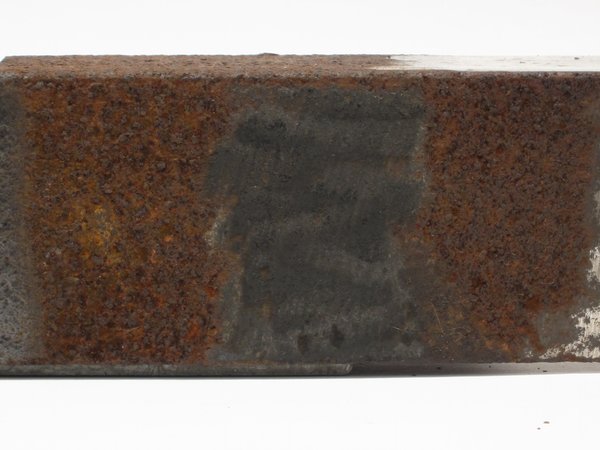
A flap wheel isn't sufficient for removing heavy rust. It's more suited for finer metal sanding and finishing.
Angle Grinder Grinding Wheel Sample
We get right down to bare, shiny metal quickly. This wheel left some pretty heavy gouges in the metal. It won’t look good, but for a functional piece this doesn’t matter. Note that we’ve ground out the pitting caused by the corrosion process. This means that we’ve also reduced the overall thickness of the workpiece in those spots. You generally should not be grinding out 1/8” deep pits on 1/4” material, since you’re reducing the strength of that area to 1/8”. The regular grinding wheel is also great for grinding off mill scale, which is the dull gray “coating” that comes on a lot of commonly available metal.
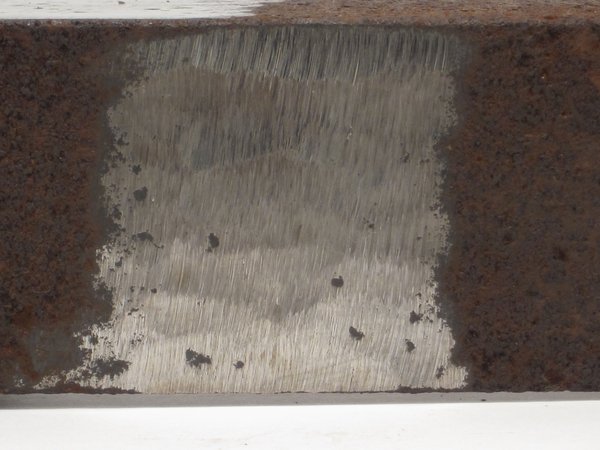
The grinding wheel is very effective at cleaning rust down to bare metal, but it tends to leave a rough surface and can result in a lot of material removal if you aren't careful.
Grinding Wheel then Flap Disc Sample
First we used a regular grinding wheel, then ran over it with a flap disc. The workpiece still has a little gouging, but most of the shallow ones were “buffed” out. The finish is much smoother to the touch than the grinding wheel alone. Unlike the grinding-wheel-only sample, this would look pretty good with a coat of paint on it. A production piece with a totally smooth finish (think of a welded plate-style bumper with smooth corners) would likely use a less aggressive grinding wheel (shallower gouging) followed up by a flap wheel.
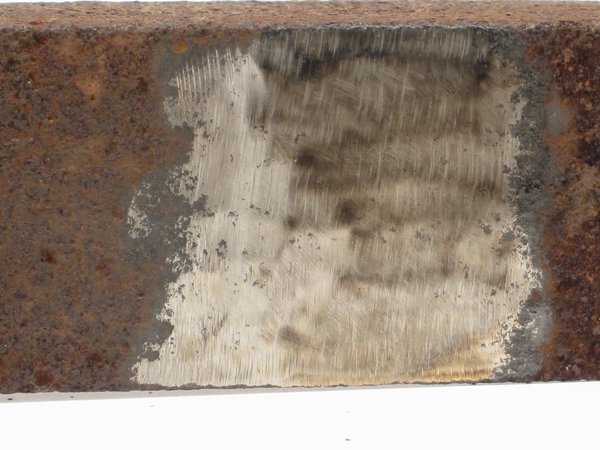
Using the flap disc after the coarser grinding wheel makes the steel much smoother.
Angle Grinder Cutoff Wheel Sample
This is just a straight cut with a cutoff wheel. When through-cutting, you must beware of how the cut piece moves so that it does not pinch the cutoff wheel or kick into the wheel when it falls. For pieces of this size and larger, it is safer to use a chopsaw, bandsaw, or hacksaw (it ain’t so bad!). This wheel is 0.045” thick, so it makes a slightly faster, thinner cut than thicker 1/8” (0.125”) wheels. It’ll also shatter more easily.
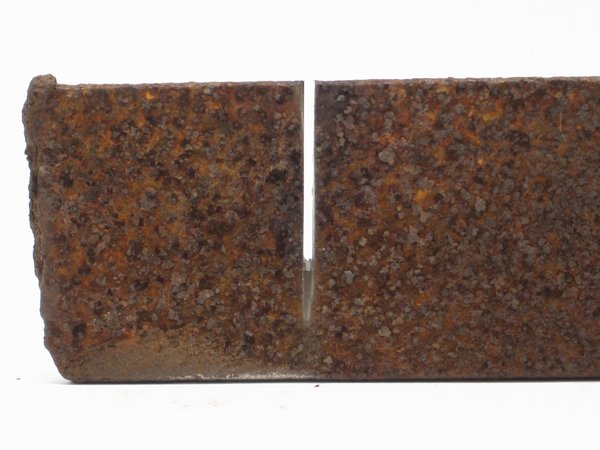
Cutoff wheels should only be used for cutting. Don't use the front or back face of the wheel for cutting, or you run the risk of weakening the wheel and causing it to shatter.
Last updated: June 3, 2019